Porosity in Welding: Identifying Common Issues and Implementing Ideal Practices for Avoidance
Porosity in welding is a pervasive problem that typically goes undetected up until it creates considerable problems with the honesty of welds. In this discussion, we will explore the key factors adding to porosity development, analyze its damaging impacts on weld performance, and discuss the finest techniques that can be embraced to minimize porosity incident in welding processes.
Usual Causes of Porosity

An additional regular culprit behind porosity is the presence of contaminants externally of the base metal, such as oil, oil, or corrosion. When these impurities are not effectively eliminated prior to welding, they can evaporate and become trapped in the weld, creating issues. Making use of filthy or wet filler products can present pollutants into the weld, contributing to porosity concerns. To alleviate these typical reasons for porosity, comprehensive cleansing of base steels, appropriate shielding gas option, and adherence to ideal welding parameters are important techniques in attaining premium, porosity-free welds.
Impact of Porosity on Weld Top Quality

The existence of porosity in welding can significantly jeopardize the structural stability and mechanical residential or commercial properties of bonded joints. Porosity creates gaps within the weld metal, deteriorating its total stamina and load-bearing capacity. These spaces work as tension focus points, making the weld much more at risk to breaking and failure under applied lots. Furthermore, porosity can lower the weld's resistance to corrosion and other ecological variables, even more reducing its long life and performance.
Among the key consequences of porosity is a decline in the weld's ductility and strength. Welds with high porosity degrees tend to display reduced impact strength and decreased capability to warp plastically before fracturing. This can be especially concerning in applications where the welded elements undergo dynamic or cyclic loading conditions. Porosity can restrain the weld's ability to effectively transmit pressures, leading to early weld failing and prospective security risks in crucial structures. What is Porosity.
Ideal Practices for Porosity Avoidance
To improve the architectural honesty and high quality of bonded joints, what certain steps can be implemented More hints to decrease the incident of porosity during the welding procedure? Porosity prevention in welding is crucial to make certain the stability and strength of the last weld. One effective method appertains cleaning of the base steel, removing any kind of pollutants such as corrosion, oil, paint, or wetness that can result in gas entrapment. Guaranteeing that the welding tools is in excellent condition, with tidy consumables and appropriate gas circulation rates, can likewise significantly minimize porosity. Additionally, maintaining a secure arc and managing the welding criteria, such as voltage, current, and take a trip speed, assists develop a consistent weld swimming pool that decreases the danger of gas entrapment. Making use of the correct welding strategy for the certain material being you can try these out bonded, such as changing the welding angle and weapon position, can additionally protect against porosity. Regular assessment of welds and immediate remediation of any type of concerns identified during the welding procedure are crucial practices to stop porosity and generate high-quality welds.
Significance of Correct Welding Techniques
Executing correct welding techniques is critical in making certain the structural integrity and top quality of bonded joints, developing upon the foundation of effective have a peek at this site porosity avoidance actions. Welding methods directly affect the total strength and sturdiness of the bonded framework. One key facet of appropriate welding methods is maintaining the proper warmth input. Too much warmth can lead to enhanced porosity as a result of the entrapment of gases in the weld pool. Conversely, inadequate heat may result in incomplete fusion, creating possible weak points in the joint. In addition, making use of the appropriate welding parameters, such as voltage, current, and take a trip rate, is crucial for achieving sound welds with marginal porosity.
Moreover, the option of welding process, whether it be MIG, TIG, or stick welding, should straighten with the specific demands of the task to ensure ideal results. Correct cleansing and preparation of the base steel, in addition to selecting the appropriate filler material, are also crucial elements of efficient welding techniques. By adhering to these finest methods, welders can reduce the threat of porosity formation and produce top quality, structurally sound welds.
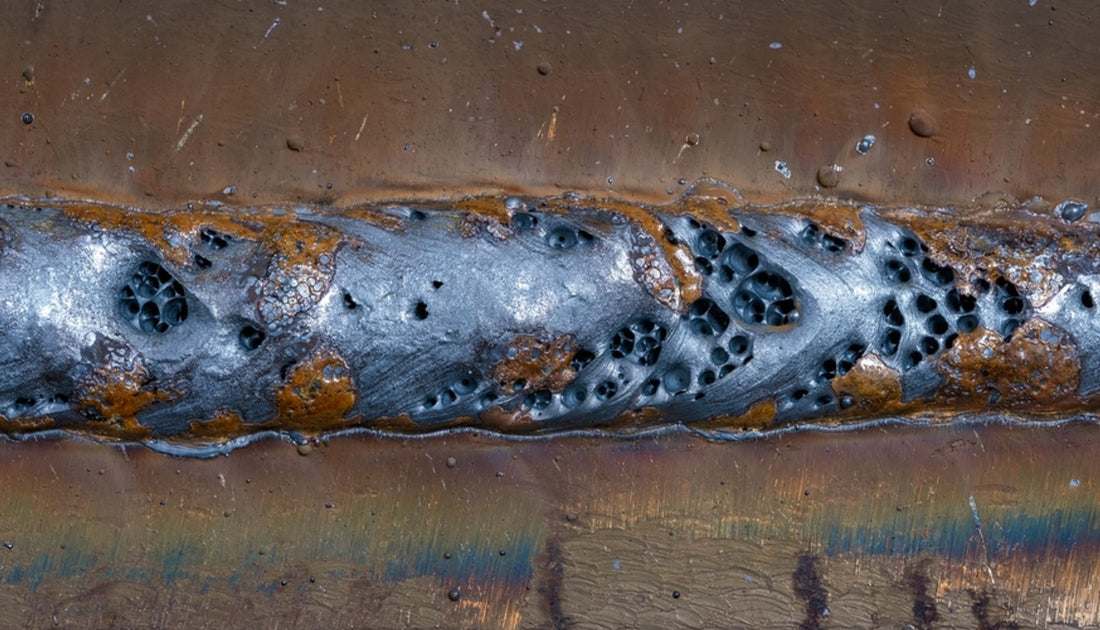
Examining and Quality Assurance Procedures
Testing treatments are crucial to spot and avoid porosity in welding, guaranteeing the strength and resilience of the final product. Non-destructive screening approaches such as ultrasonic testing, radiographic screening, and aesthetic evaluation are typically used to recognize possible flaws like porosity.
Post-weld examinations, on the various other hand, examine the final weld for any issues, including porosity, and verify that it fulfills specified requirements. Applying a comprehensive high quality control strategy that includes comprehensive screening treatments and inspections is critical to minimizing porosity issues and guaranteeing the general high quality of bonded joints.
Verdict
To conclude, porosity in welding can be a common problem that impacts the top quality of welds. By identifying the typical reasons for porosity and executing ideal methods for avoidance, such as appropriate welding strategies and screening actions, welders can make certain premium quality and reliable welds. It is important to focus on prevention approaches to reduce the event of porosity and maintain the integrity of bonded frameworks.